
Is Design-Build Right for My Project?
Introduction to Design-Build vs. Design-Bid-Build
As you embark on your next project, one of the first major decisions you’ll face is selecting the right project delivery method. The two basic approaches are Design-Bid-Build (DBB) and Design-Build (DB).
Traditionally, Design-Bid-Build (DBB) has been the standard approach, where the owner contracts separately with an architectural/engineering (A/E) firm to develop the design independently of contractor input. Once the design is fully developed, the owner solicits bids from multiple general contractors (GCs), typically selecting the lowest-cost GC. This method often requires the owner to manage communication between the design firm and the contractor, which can lead to miscommunications, delays and cost overruns.
Design-Build (DB) consolidates both design and construction responsibilities under a single contract. The owner engages with Design-Build firms capable of fulfilling both A/E and GC roles at the project onset. The integrated nature of Deign-Build fosters potential cost savings through streamlined communication and proactive problem-solving. By involving designers and builders from the project’s inception, potential issues are identified and resolved early, minimizing expensive changes and delays. This unified approach ensures optimal design quality and construction feasibility, ultimately delivering a project that achieves a balanced alignment of cost, quality and schedule, offering greater overall value.
How Do I Know if Design-Build is Right for My Project?
Each project is unique and requires careful evaluation to determine the right delivery method. Design-Build may be particularly advantageous in the following scenarios:
Fast-Track Projects
When time is of the essence, Design-Build can accelerate project delivery. The overlap of design and construction phases enables work to begin before the design is finalized, reducing the overall project timeline.
Complex Projects
For complex projects or projects with unique design requirements, having both the design and construction teams under one contract allows for seamless collaboration and quick resolution of design issues.
Client Involvement
Clients who prefer to be less involved in day-to-day project management may find Design-Build advantageous. With one entity responsible for both design and construction, clients can focus on key decisions without the need to manage multiple contracts. This single point of responsibility streamlines communication and accountability.
Benefits of the Single GBA Team Approach on Design-Build Projects
Leveraging the combined expertise of GBA and GBA Builders, our integrated design-build approach offers several advantages that enhance project outcomes. The streamlined process fosters collaboration and ensures that both design and construction teams align their goals, ultimately delivering greater value to our clients.
1. Efficient Internal Communication
With GBA and GBA Builders operating under one roof, real-time collaboration and rapid issue resolution are natural outcomes. Our long history of working together builds familiarity and trust. GBA Builders can provide practical feedback on design constraints, schedules, and costs, ensuring practical and feasible designs. Additionally, early involvement from the construction team ensures continuous cost control and budget adherence.
GBA Builders’ ability to work alongside the engineers allows for determining the best design options to maintain project budget and schedule. This close collaboration enables real-time adjustments and optimizations that ensure constructability and efficiency. Conversely, GBA can work directly with GBA Builders to refine designs based on construction feedback, resulting in a more cohesive and well-integrated project. This synergy between GBA and GBA Builders’ expertise ensures that projects are not only designed to meet aesthetic and functional goals but are also optimized for cost-effectiveness and timely completion.
2. Improved Customer/Client Service
Clients interact with a single entity, simplifying communication and reducing the potential for misunderstandings. A single prime contract minimizes administrative burden and oversight complexities, allowing for more direct communication between designers and builders without the client acting as an intermediary.
3. Enhanced Accountability
Accountability is ingrained in the GBA culture. We are committed to your project’s success, ensuring cohesive and aligned efforts. As part of the same company, GBA and GBA Builders share a common goal of project excellence, driving higher performance standards.
4. Internal Growth Opportunities
The GBA team approach offers significant internal growth opportunities. By working together early in their careers, team members develop trust and efficiency, leading to high-quality project delivery that benefits clients in the long term. Engineers gain valuable exposure to the construction side, while construction professionals learn to see the engineering perspective. This cross-disciplinary understanding helps our projects benefit from a more comprehensive view of the challenges and opportunities from both perspectives, fostering a culture of continuous improvement and excellence in project execution.
Design-Build May Be the Best Value for Your Project
There are often concerns that Design-Build won’t yield the lowest initial cost and could potentially create conflicts of interest. Design-build shifts more risk to the contractor, as they take responsibility for both the design and construction. This encourages the contractor to work with the engineer to optimize designs for cost-efficiency and constructability, ultimately reducing the owner’s risk exposure.
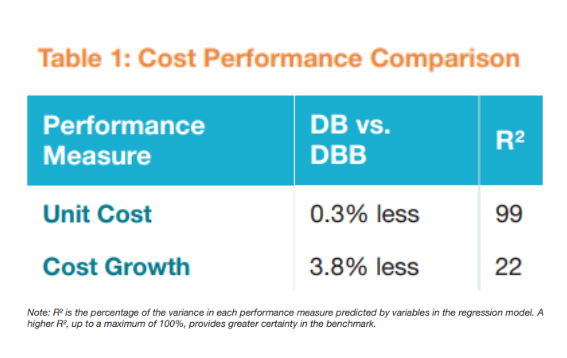
Utilizing contract types like Cost-Plus Guaranteed Maximum Price (CPGMP) with shared savings ensures a strong focus on cost reductions. Strategic partnerships with trades ensure quality and time savings while competitive bidding on other scopes maintains cost efficiency. The inherent time savings in DB projects often offset potential higher costs and integrated constructability efforts ensure continuous value engineering without extending timelines.
According to the report by the Charles Pankow Foundation and Construction Industry Institute in Table 1, Design-Build’s cost performance is comparable to or even lower than Design-Bid-Build (DBB) in terms of total capital cost and potential cost growth. This is contrary to the commonly held belief that DB projects are more expensive than DBB projects.
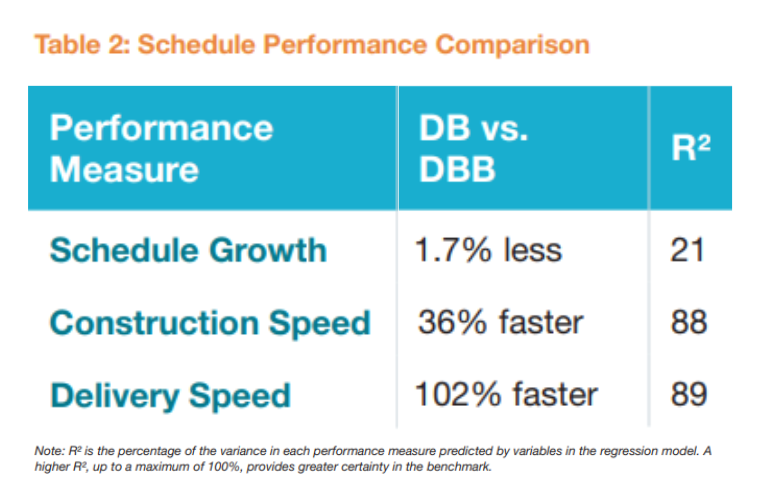
Similarly, Table 2 highlights the benefits of DB compared to DBB in terms of project schedule. While the two delivery methods have negligible differences in project schedule growth. Design-Build is objectively faster in terms of construction speed (construction phase only) and delivery speed (from design initiation to construction completion), in most cases.
Design-Build in Action
GBA and GBA Builders have a long history of successful collaboration on numerous projects. This partnership leverages the strengths of both entities, creating a unified team that enhances project delivery by seamlessly integrating the design and construction phases.
An example of this great partnership shines through a recent vaccine compounding and aseptic filling suite building expansion. GBA and GBA Builders were entrusted with the design and construction of a multi-level building within a one-year timeframe to facilitate the manufacturing and filling of a critical vaccine amid a global supply chain crisis. The project aimed to address the urgent need for increased production capacity and modernization of the facility. The new building expansion consisted of three levels, including a basement for utility generation equipment, a first-floor production area with a new aseptic fill/finish suite containing a vial filler within an isolator, compounding suite, tank wash and prep rooms, and a second-floor mechanical area with a new substation and mechanical support equipment.
GBA’s role included evaluating existing mechanical and process utility systems to connect and extend to the new expansion. The design also encompassed a new water for injection (WFI) loop with point-of-use (POU) coolers, a clean-in-place (CIP) system with a new CIP skid serving multiple users, a chilled water system with a new air-cooled chiller and multiple new HVAC systems.
On the construction side, GBA Builders managed the completion of the 17,700-SF, $46 million dollar expansion. All construction work was performed while the facility remained fully occupied and operational. Each phase of construction was isolated from the occupants by fire-rated/cleanroom construction barriers and a negative air environment to preclude any airborne contaminants/particulate matter, micro-organisms and dust from infiltrating into the occupied and cleanroom spaces.
The Design-Build approach was crucial for this project, allowing for early ordering of long-lead equipment and a multiple package approach to meet the tight schedule. This method facilitated real-time collaboration between GBA’s design team and GBA Builders’ construction team, ensuring efficient communication and quick resolution of issues. The seamless integration of design and construction phases enabled the project to be completed within the required timeframe, demonstrating the effectiveness of the Design-Build approach in delivering high-quality, complex projects.
Conclusion
The partnership between GBA and GBA Builders exemplifies the advantages of the Design-Build approach, demonstrating significant benefits in communication efficiency, client service, accountability and cost management. As the construction industry continues to evolve, these integrated collaborations are poised to lead the way in delivering successful, high-quality projects.
Bryan Chau
Brenna Acord-Morris
Brenna began her career as a mechanical engineer in the Life Sciences group, specializing in HVAC, hydronic piping and plumbing designs. She is an Assistant Project Manager, collaborating to deliver successful outcomes on projects ranging from feasibility studies to large-scale design-builds.